Marcopol
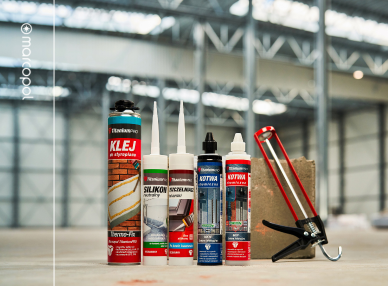
Kotwy chemiczne Titanium od Marcopolu – profesjonalne mocowanie w betonie
Dowiedz się więcej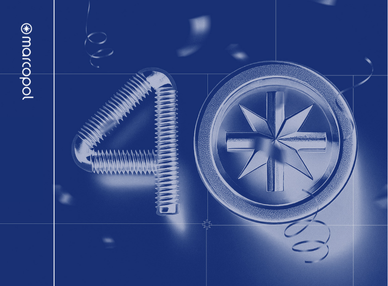
Rozstrzygniecie konkursu na 40-lecie Marcopolu!
Dowiedz się więcej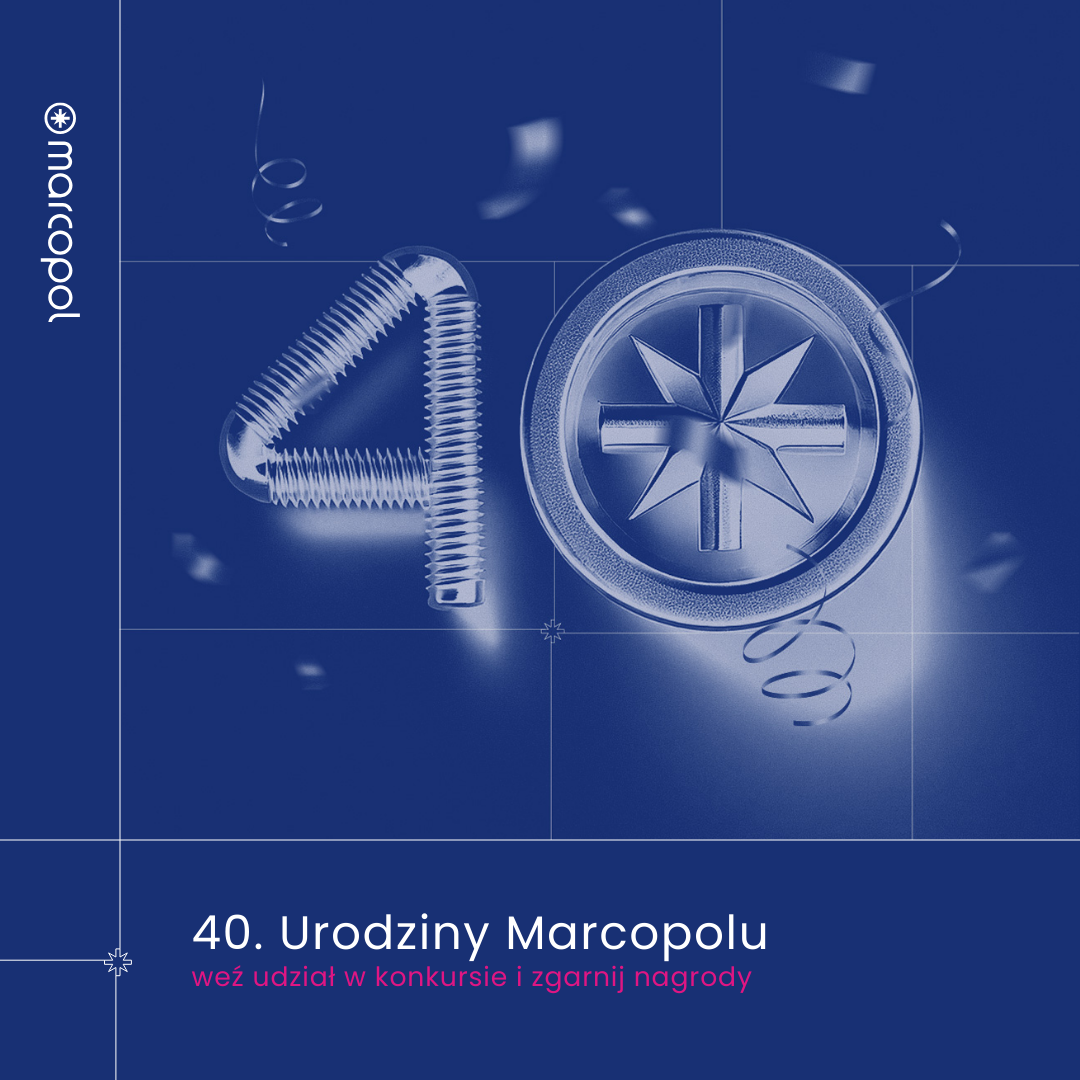
40 lat Marcopolu: Świętuj z nami i wygrywaj!
Dowiedz się więcej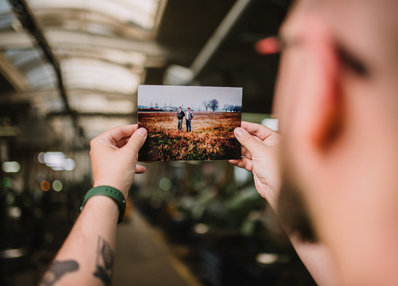
Cztery dekady doskonałości w branży elementów
Dowiedz się więcej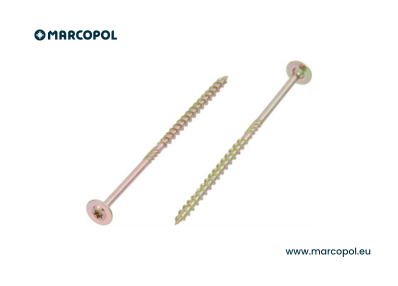
Jakie są najlepsze sposoby łączenia belek drewnianych?
Dowiedz się więcej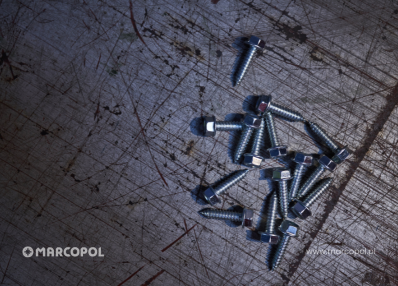
Rodzaje śrub – klasa, oznaczenia, normy i wytrzymałość
Dowiedz się więcej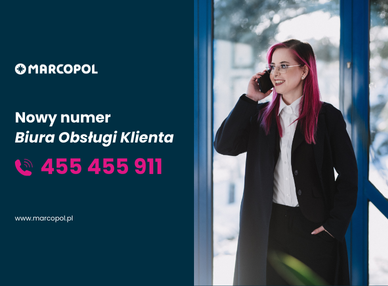
Potrzebujesz pomocy? Zadzwoń do nas!
Dowiedz się więcej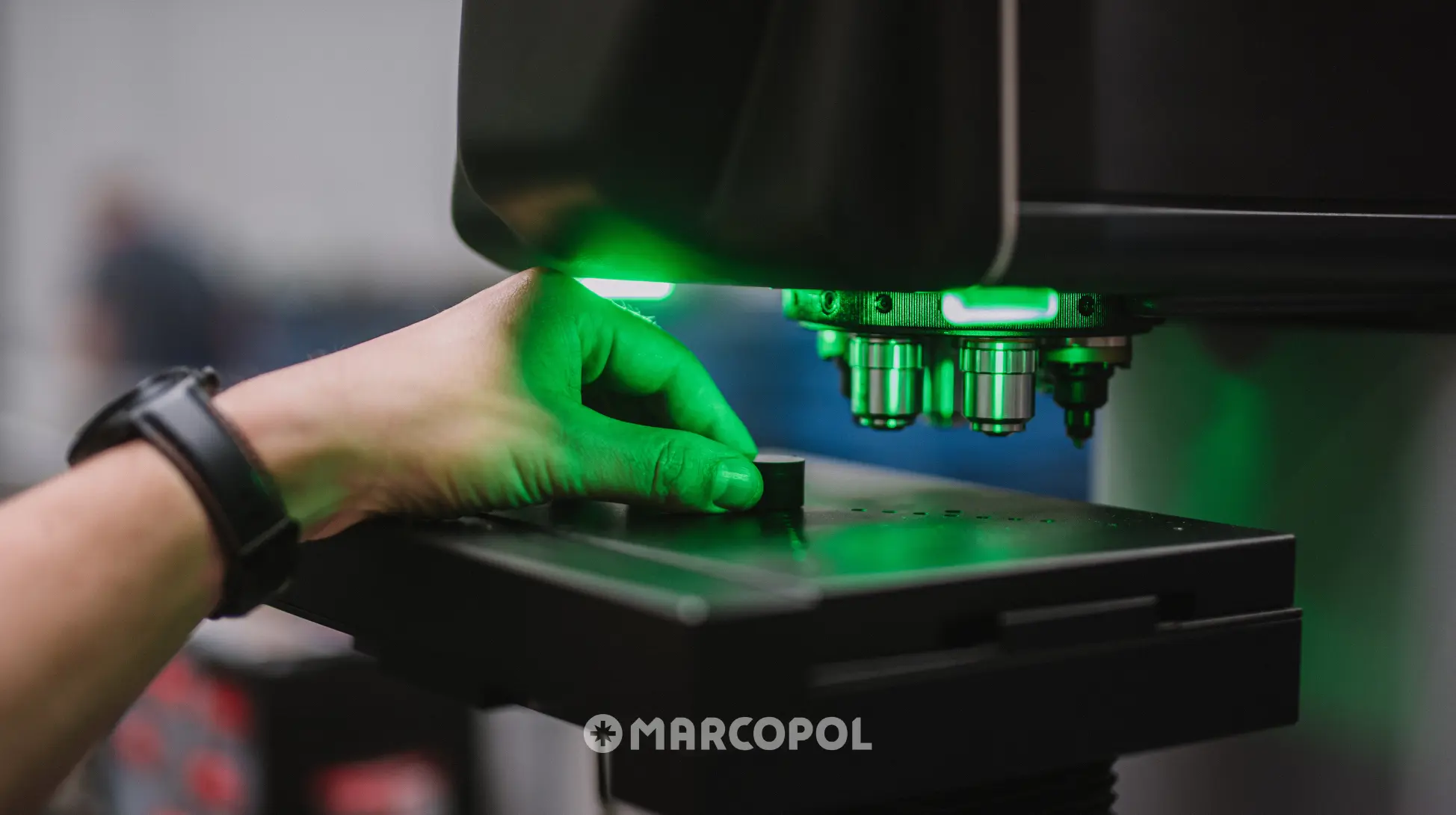
Zrozumienie i zastosowanie śrub DIN 931 zgodnie z normą ISO 4014
Dowiedz się więcej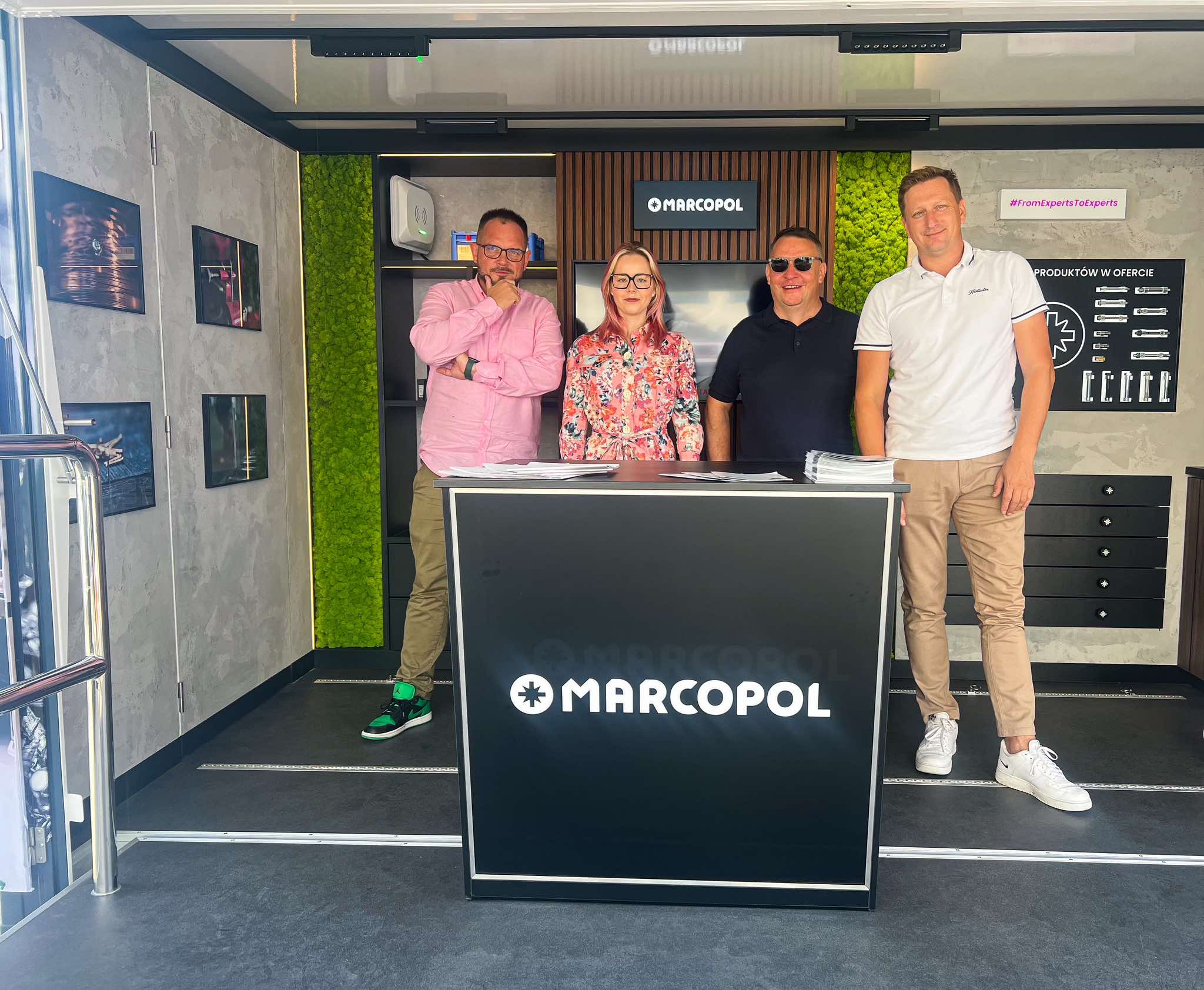
Relacja z Targów Majster 2024. Mobilny Showroom w akcji!
Dowiedz się więcej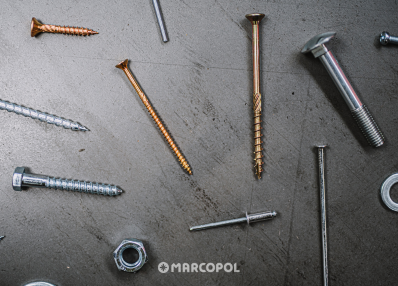
Przegląd łbów w elementach złącznych (cz. 1)
Dowiedz się więcej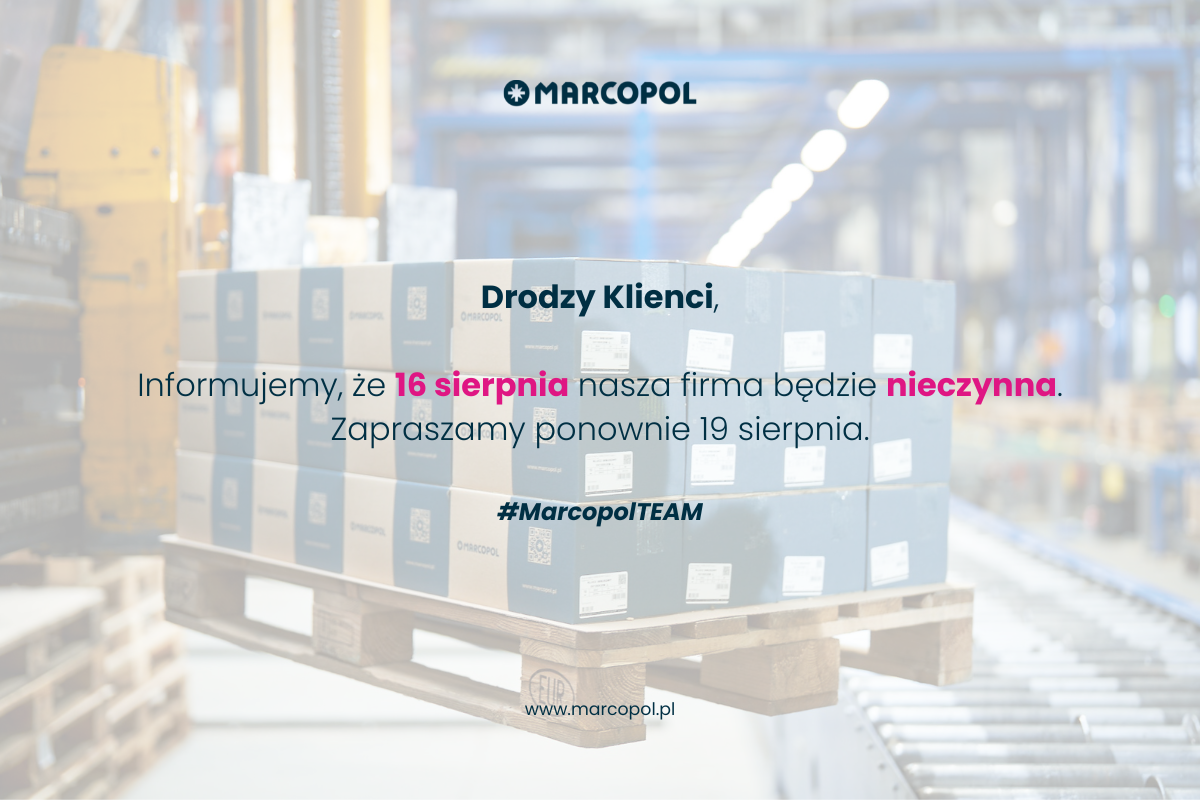
Informacja dla Klientów
Dowiedz się więcej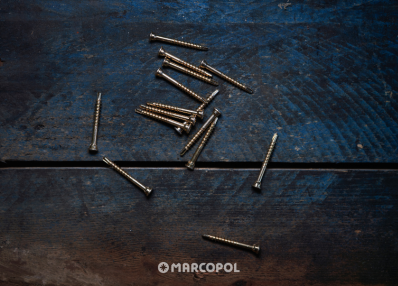
Wkręty konstrukcyjne do więźby dachowej z łbem cylindrycznym Marcopol – niezawodność i trwałość dla profesjonalistów
Dowiedz się więcej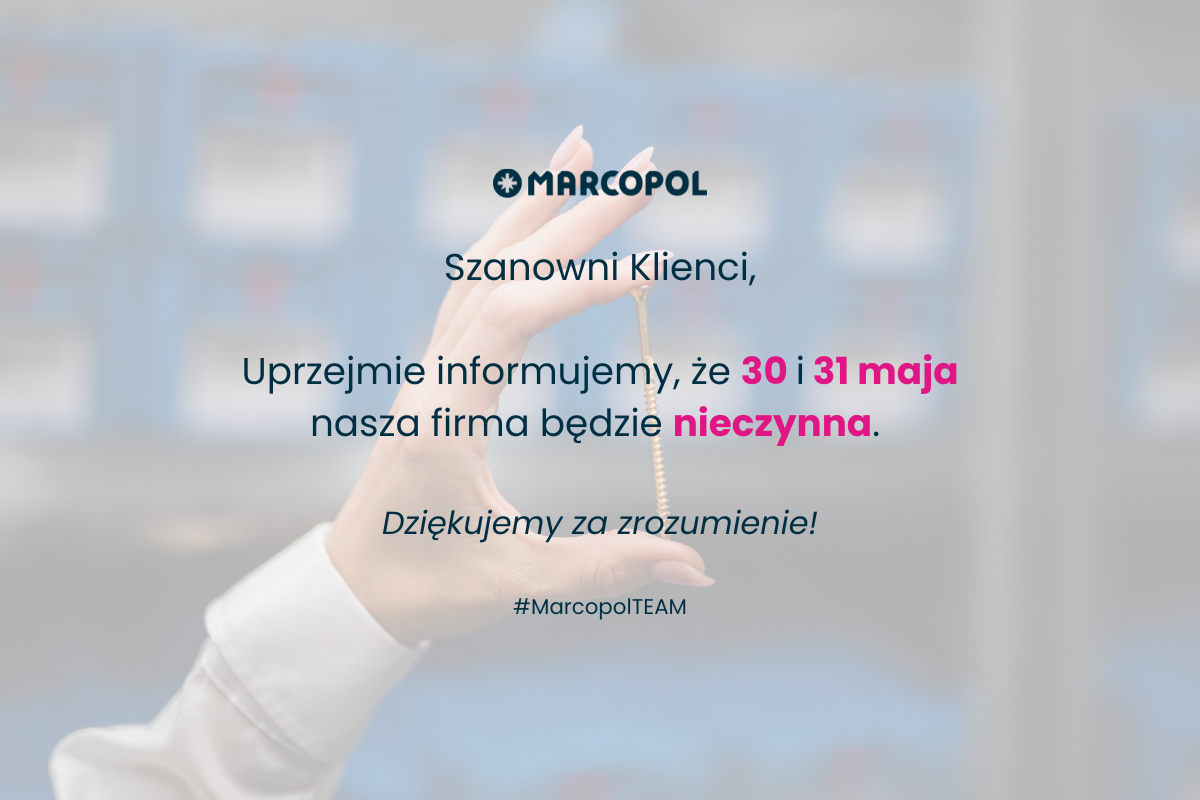
Informacja dla klientów
Dowiedz się więcej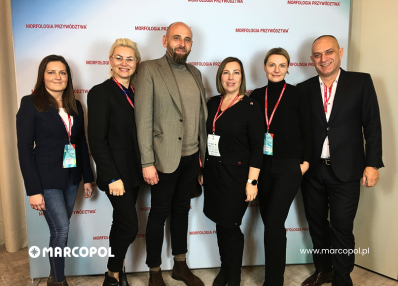
Marcopol na “Morfologii przywództwa”
Dowiedz się więcej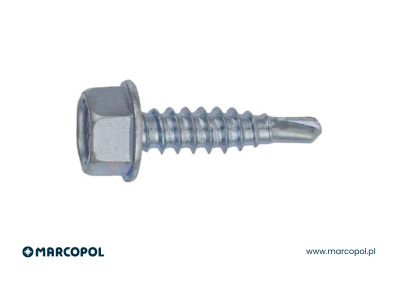
Wkręty farmerskie Marcopol. Jakość na lata
Dowiedz się więcej
Marcopol. Coraz bliżej IATF
Dowiedz się więcej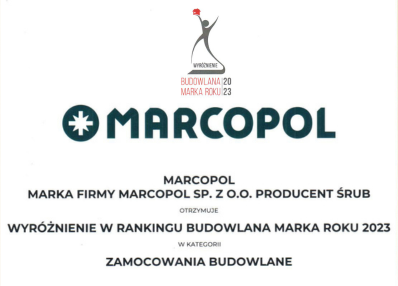
Marcopol wyróżniony w rankingu “Budowlana Marka Roku 2023”
Dowiedz się więcej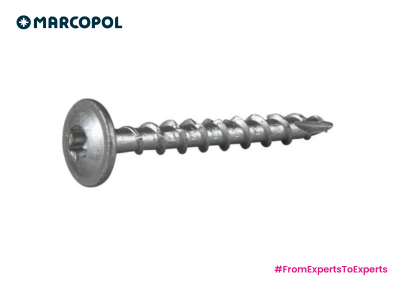
Kryteria wyboru odpowiednich łączników ciesielskich – przewodnik po naszej ofercie
Dowiedz się więcej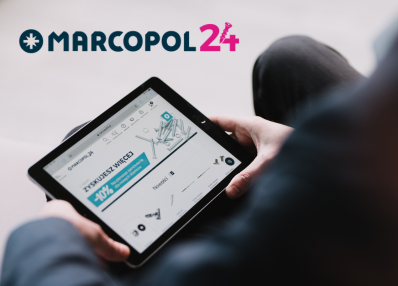
Marcopol24.pl. Efektywnie dobieraj rozwiązania!
Dowiedz się więcej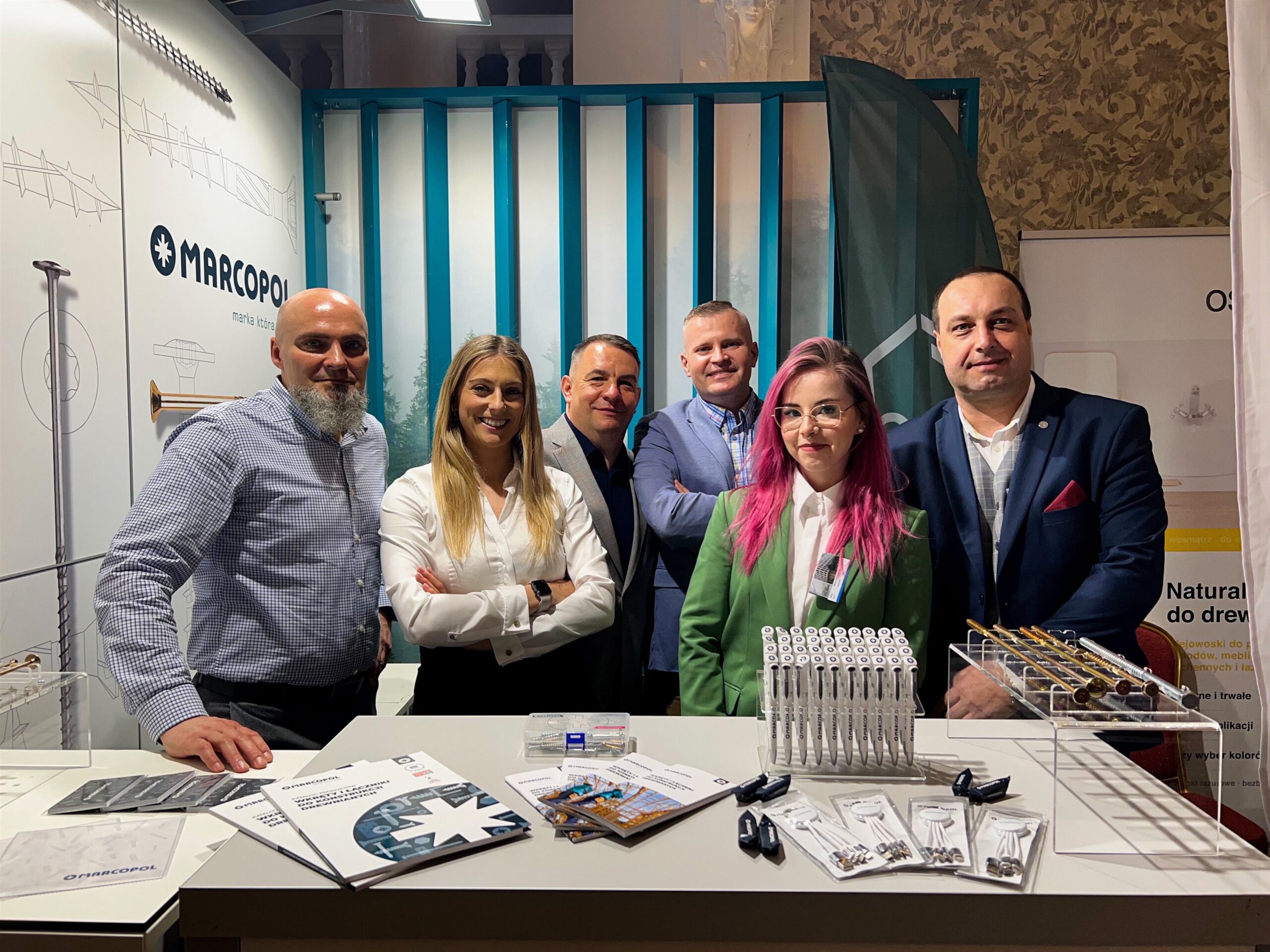
Po HolzBau Forum Polska 2023
Dowiedz się więcej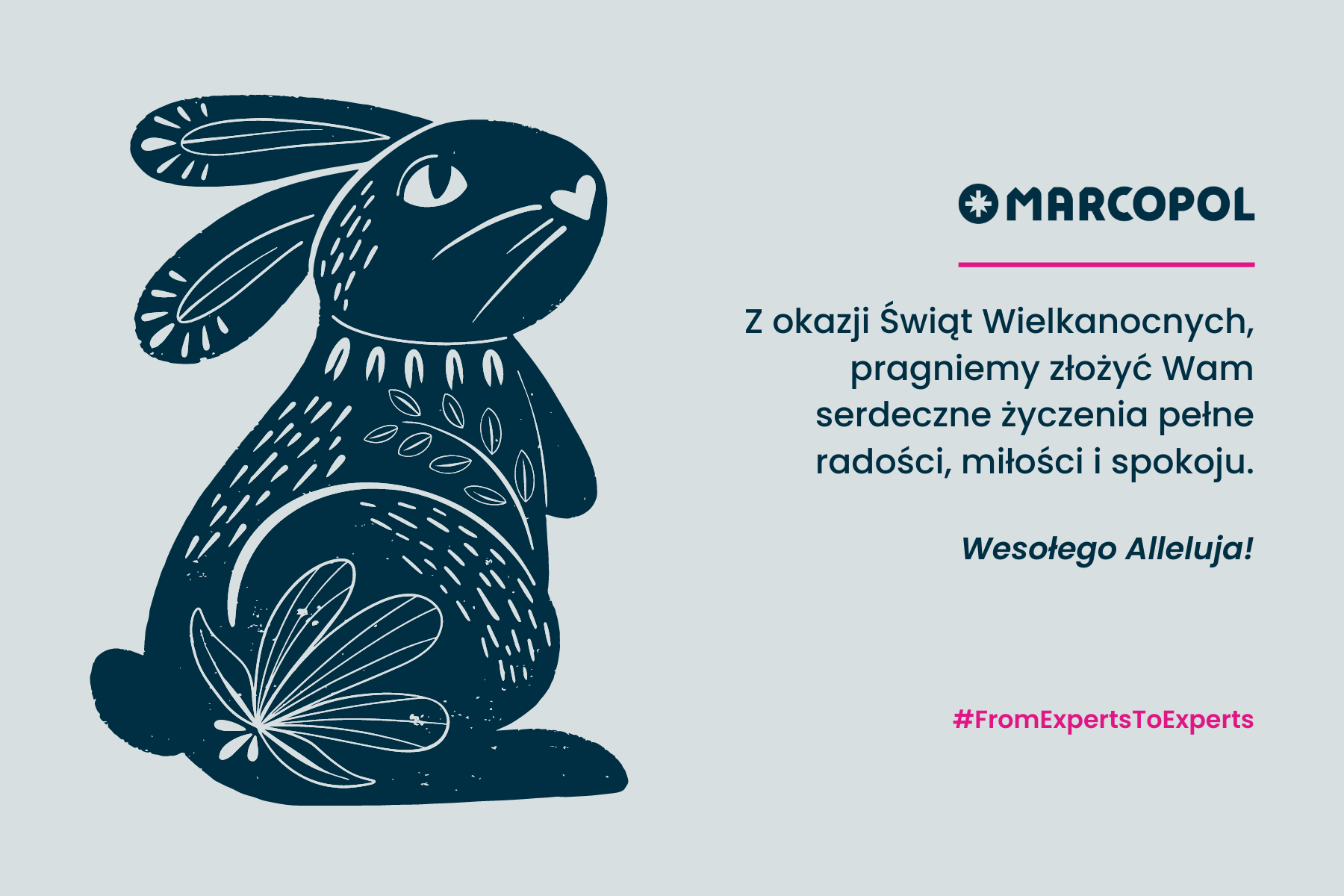
Radosnych Świąt Wielkanocnych!
Dowiedz się więcej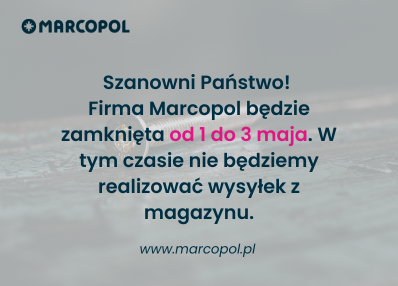
Komunikat dla klientów
Dowiedz się więcej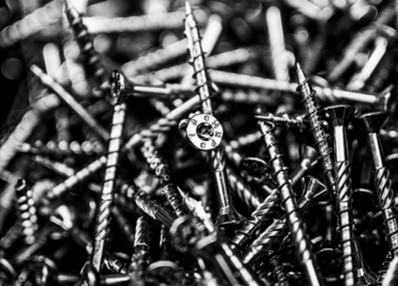
Wyzwania dla producentów elementów złącznych w 2023 roku
Dowiedz się więcej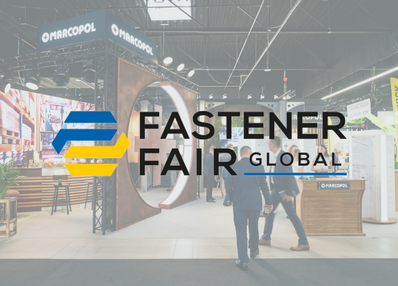
Odwiedź Marcopol na targach Fastener Fair Global 2023!
Dowiedz się więcej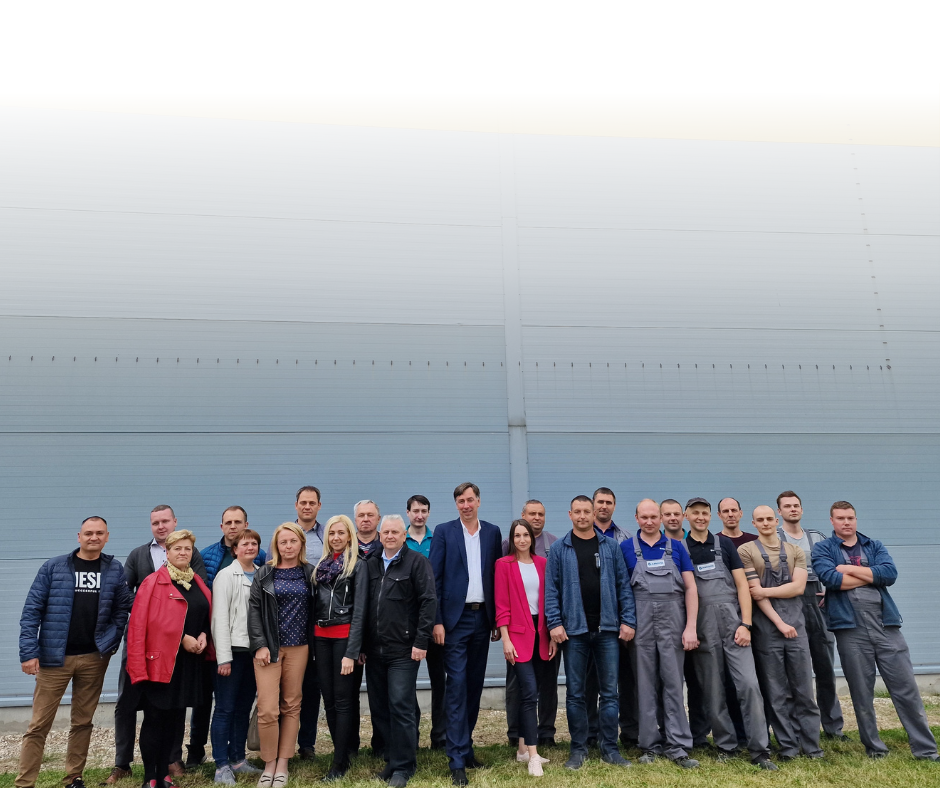
Stawiamy na dynamiczny rozwój Marcopolu w regionie
Dowiedz się więcej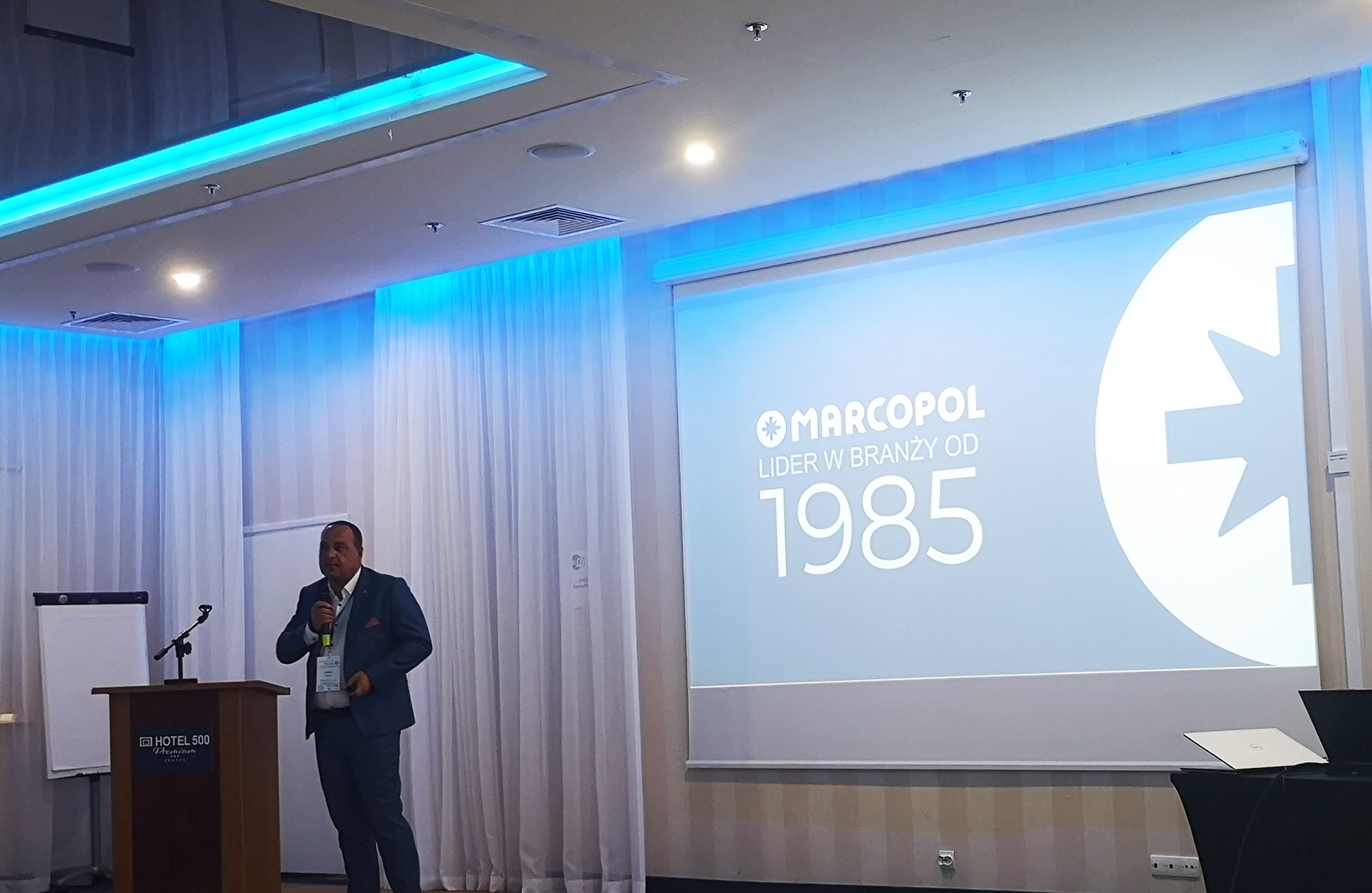
VIII Konferencja Techniczna PIKS z Marcopolem
Dowiedz się więcej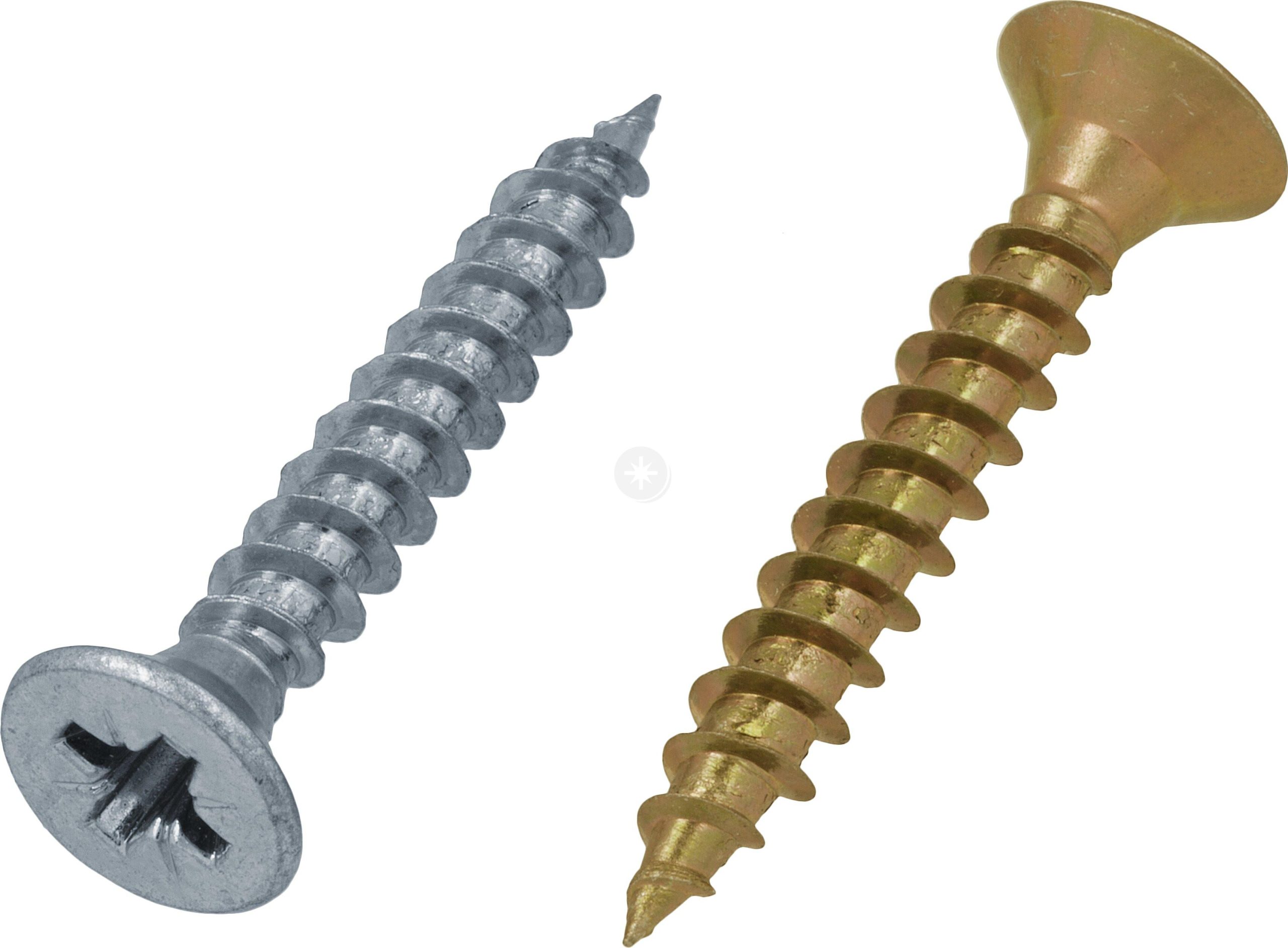
Wkręty do drewna. Wszystko, co musisz o nich wiedzieć
Dowiedz się więcej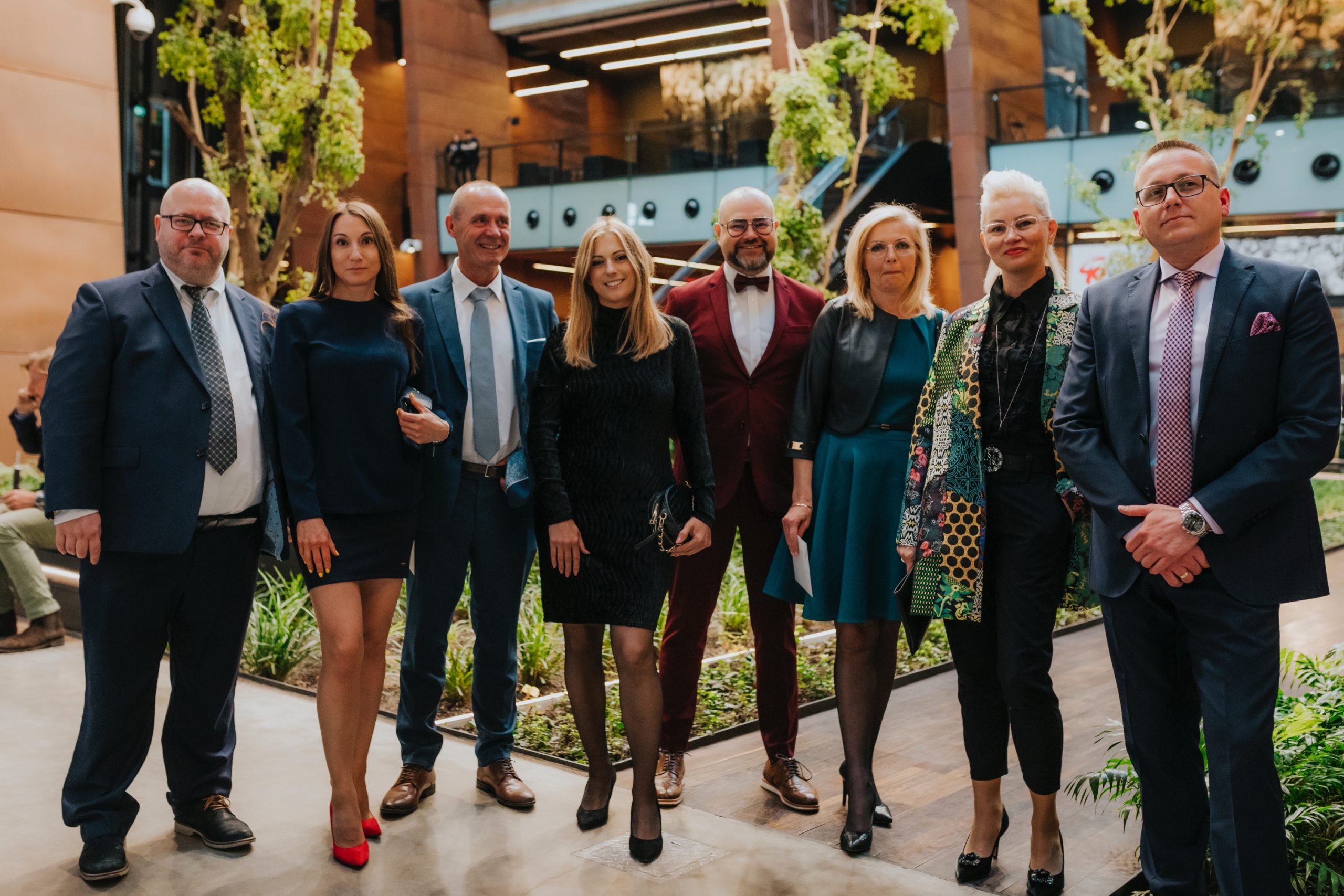
Marcopol z tytułem Pomorskiego Pracodawcy 2021
Dowiedz się więcej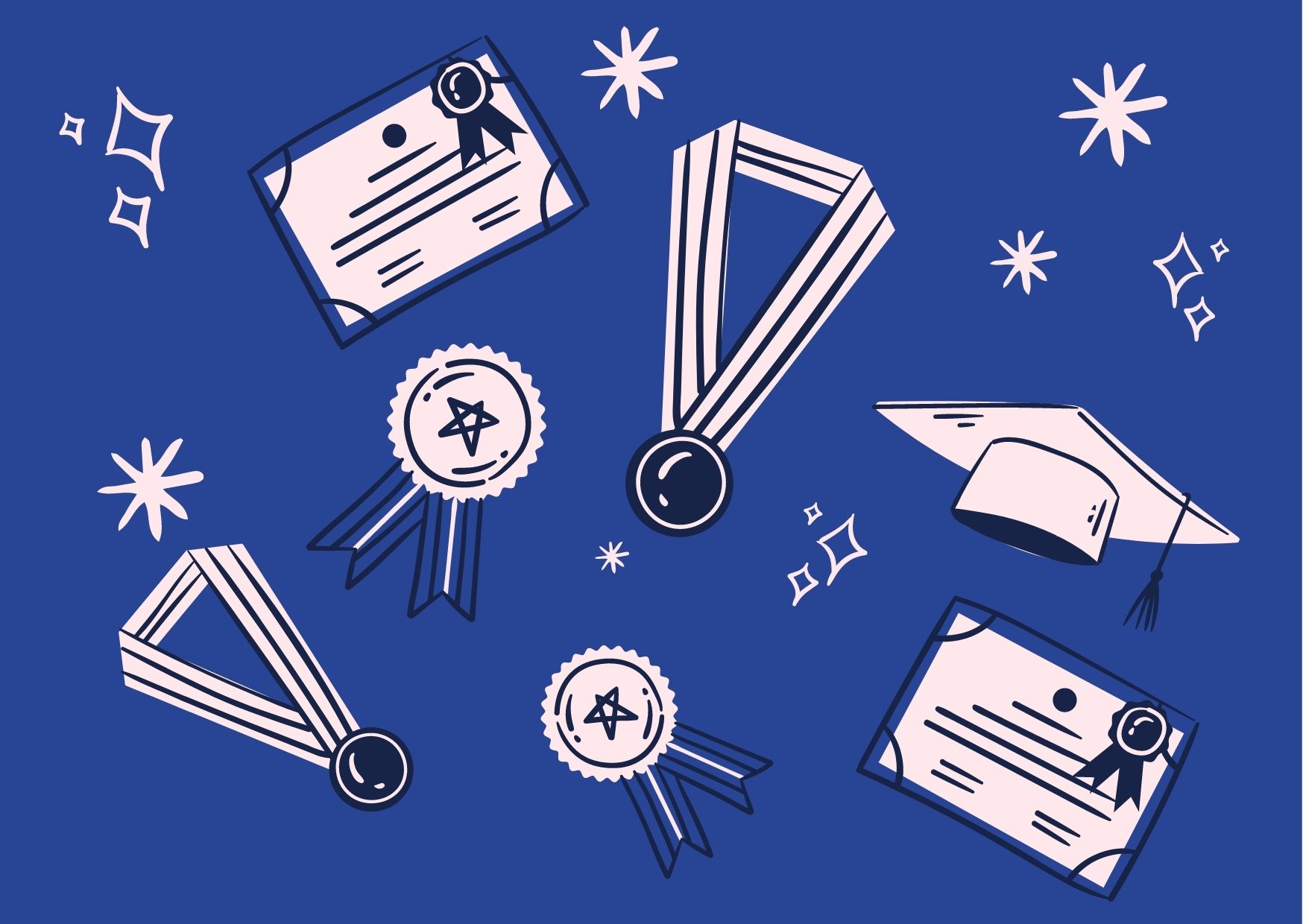
Marcopol wśród Poland’s Best Employers 2022
Dowiedz się więcej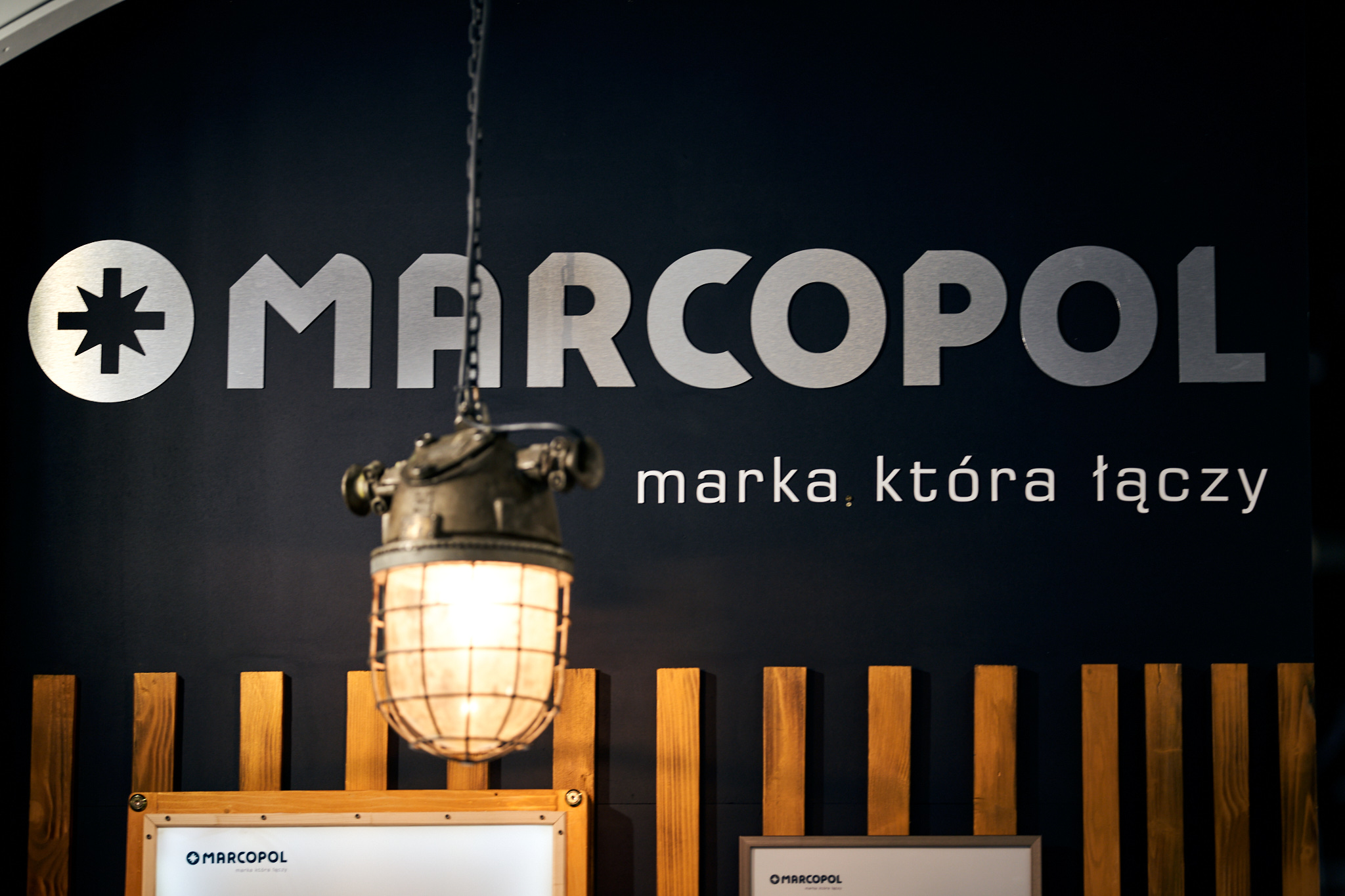
Dzielimy się wiedzą – skutecznie!
Dowiedz się więcej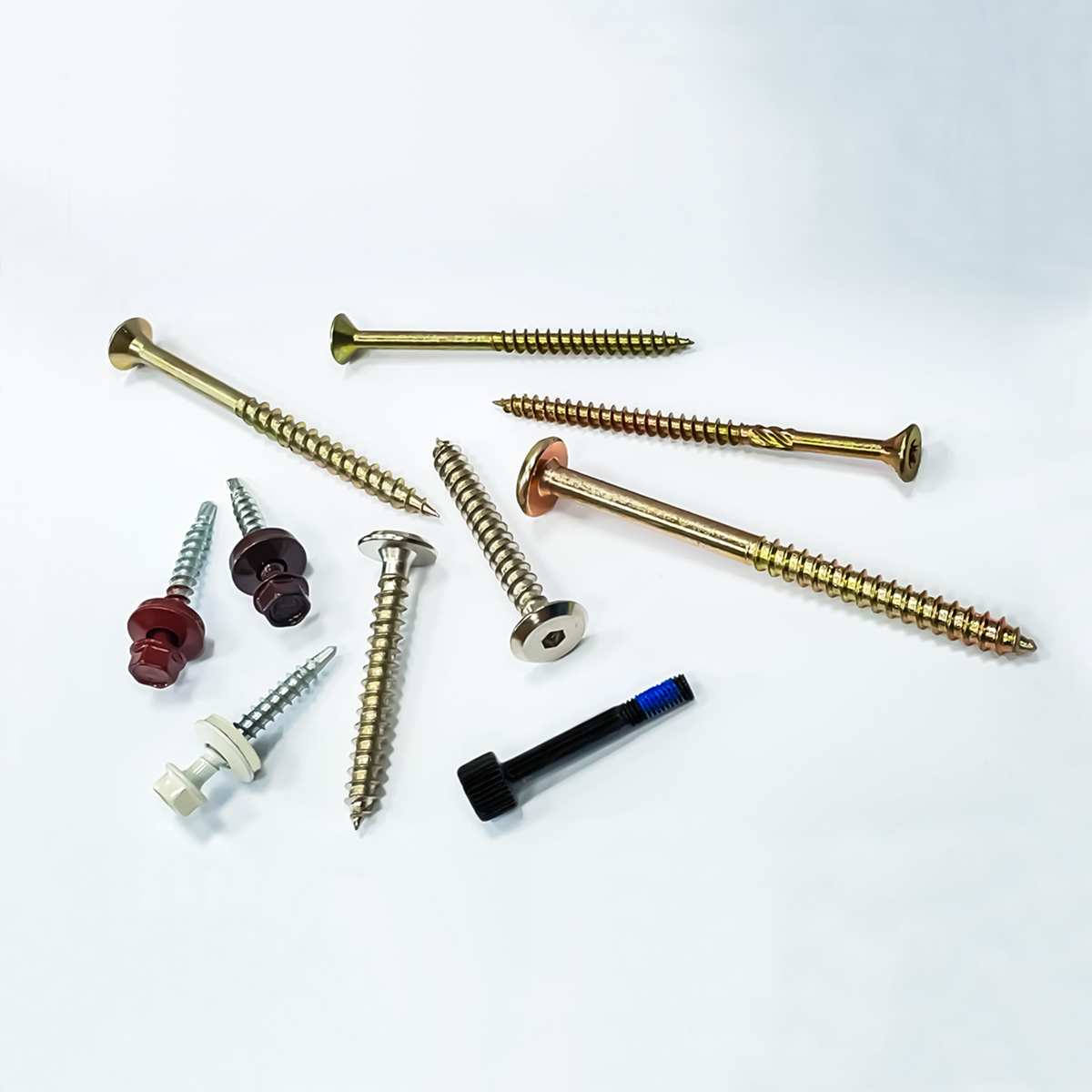
Zastosowanie wkrętów i gwoździ w konstrukcjach drewnianych
Dowiedz się więcej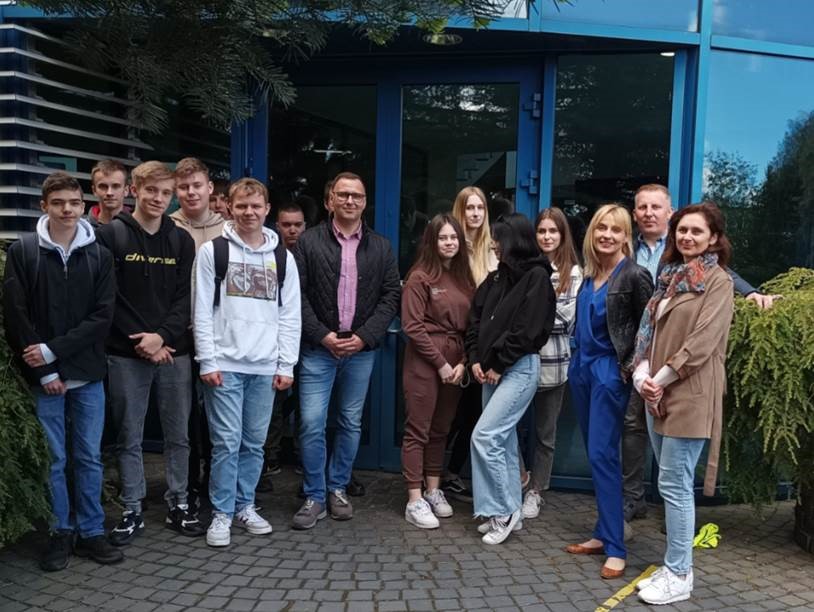
Jak wygląda logistyka w praktyce?
Dowiedz się więcej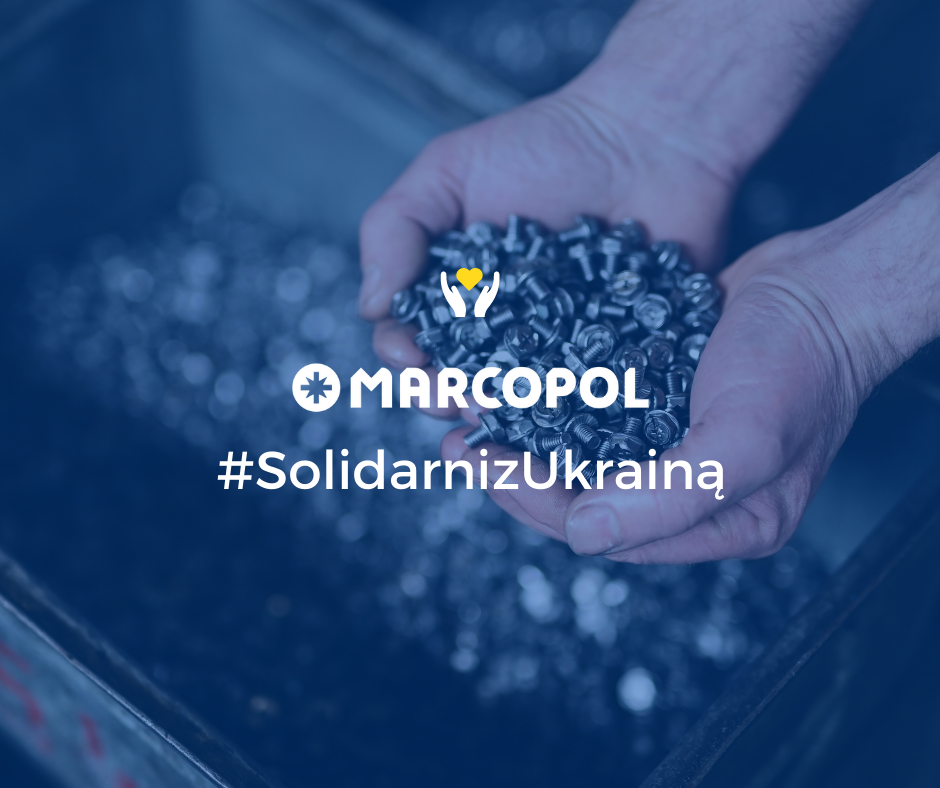
Solidarni z Ukrainą.
Dowiedz się więcej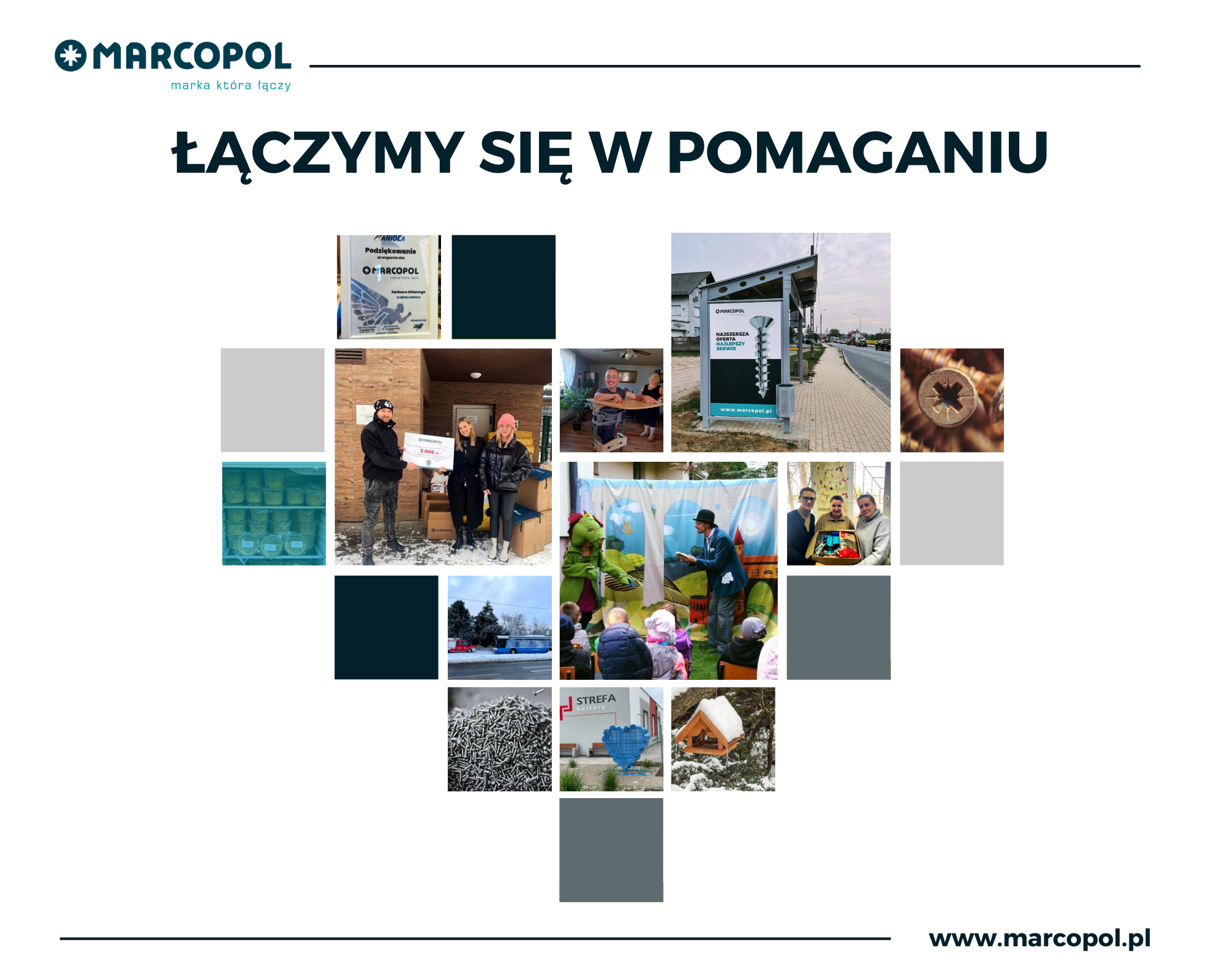
Łączymy się w pomaganiu!
Dowiedz się więcej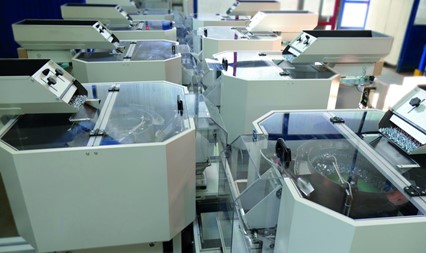